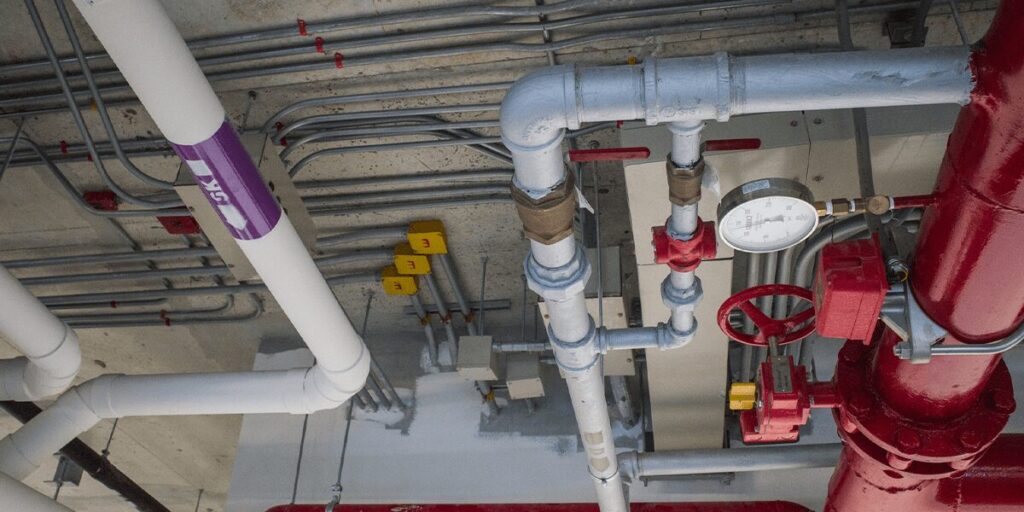
Many building materials are selected for their fire protection capabilities, but the construction process often leads to gaps between these materials, such as joints between walls and ceilings or openings for pipes. Fire stopping fills those gaps to block flames and smoke from spreading throughout a building. If you own, manage or work on a commercial building, fire stopping implementation, maintenance and testing are essential for protecting occupants and complying with building codes.
What Is Fire Stopping?
Fire stopping refers to a method of passive fire protection that fills openings and gaps between two fire-resistant materials. For example, breaking through a wall to install a pipe or cables creates a hole in the fire-resistant material. Fire stopping installs another fire-resistant material around the edges of the pipe to fill the gap.
Usually, fire stopping employs intumescent materials, which swell up when heated. During a fire, the material expands to create a tight seal between the nearby fire-resistant items. Other materials used for fire stopping include silicones, rubbers and cementitious mortars.
Some examples of openings requiring fire stopping include pipe and cable penetrations, the tops of walls, ducts, joints and slab edges. These spaces can create channels or pathways for flames and smoke to spread more easily across a building, so eliminating them can contain a fire to a smaller area.
Effective fire stopping measures can save lives while helping you comply with building codes. Some other benefits include minimizing risks to property and supporting emergency service personnel in reaching and suppressing a fire.
How Fire Stopping Works
Fire stopping starts with the concept of compartmentation, or segmenting a building into separate sections to prevent fire spread. Each of these compartments has fire-resisting structures, usually with 30-120 minutes of resistance, and fire stopping materials to address openings to the compartment.
While blocking flames is a crucial capability of fire stopping, most fire deaths come from smoke inhalation, so their smoke-stopping characteristics are just as important.
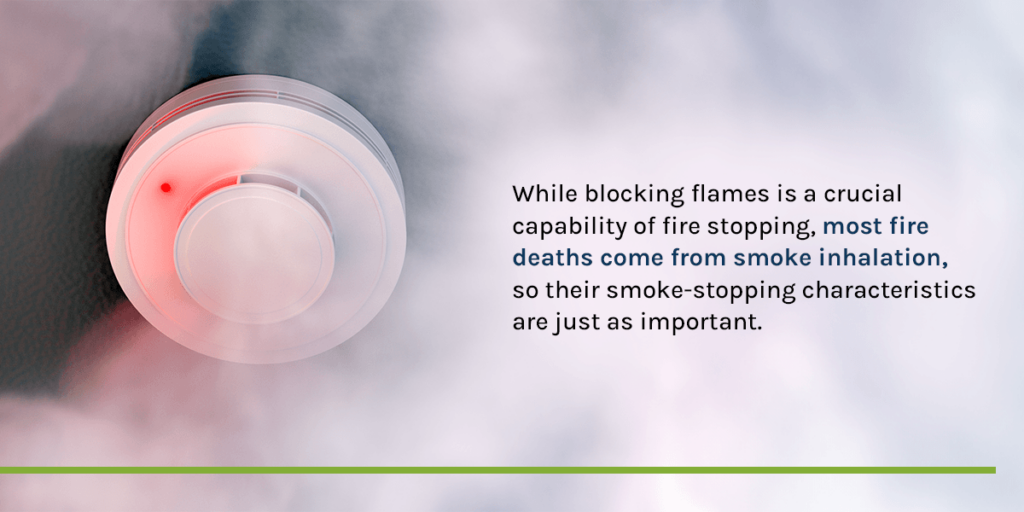
Manufacturers achieve fire resistance in many ways, but the mechanism to prevent fire spread depends on the device used. Some fire stopping devices include:
- Fire sleeves: Fire sleeves wrap around pipes and cables and are placed at their entry and exit points between compartments. They’re made of intumescent materials that expand when heated to fill in the gap between the pipe and the wall or ceiling and create a tight seal.
- Fire collars: A fire collar is similar to a fire sleeve but has a rigid metal shell containing intumescent material. During a fire, plastic pipes melt. The intumescent material in a fire collar expands inward to fill the gap created when the pipe melts. While you must install a fire sleeve within a solid material, like concrete, you can use a fire collar in other structures, like plasterboard and masonry. It has fixing lugs for secure installation.
- Fire sealants and caulks: Like their non-resistant counterparts, fire-resistant sealants and caulks apply over joints, such as walls and ceilings, but they expand to ensure complete coverage of the gap. You’ll find them on door frames, window frames and cable and pipe penetrations. Sealants and caulks may also be used with fire doors and windows.
- Fire stop pillows: A fire stop pillow also uses intumescent materials. It holds them in a cube or block that covers larger holes, such as those used for cable trays.
- Fire stop mortar: Fire stop mortar is a cementitious mortar that dries to a hard surface and absorbs heat. It can help achieve fire stopping across larger areas.
Fire Safety Regulations and Requirements
Most modern buildings must implement fire stopping to meet basic building codes, and high-risk environments like healthcare facilities and apartment complexes have stricter requirements. Retrofit projects also need to comply with fire safety regulations and requirements.
The International Building Code (IBC) and National Fire Protection Association (NFPA) requirements often refer to other standards, such as those from ASTM International. Some commonly used standards in commercial buildings include ASTM E2174 and NFPA 101.
In these standards, you can find information on where you need firestopping, labeling and material requirements and test ratings. High-risk facilities need regular testing performed by certified inspectors to confirm the system’s efficacy. Abide by standards and prioritize proactive fire stop installation and maintenance to keep occupants safe and avoid costly fines, regulatory activity or interruptions to your business.
Fire Stopping vs. Fire Blocking and Fire Proofing
Fire blocking and fire proofing are closely related terms with slightly different purposes than fire stopping.
Fire proofing aims to protect structural elements from the effects of fire through materials like spray-on coatings, insulation systems and fire-resistant boards. It affects the ability of these items to resist damage from fire. Fire blocking works similarly to fire stopping but focuses more on concealed spaces. It helps to prevent fire and smoke from spreading in concealed spaces like wall cavities and roof spaces.
All three of these methods contribute to a robust fire protection system in a building.
Implementing Fire Stopping Measures
Correctly implementing fire stopping technology requires a thorough understanding of many elements, and working with a professional can help you achieve them effectively. Some areas to consider include:
- Your application: Substrates, fire stopping devices and risk level will all contribute to selecting and implementing the most effective solutions.
- Code requirements: Similarly, your building’s characteristics, your industry, the ratings of your materials and the type of seal needed will influence which building codes you must meet.
- Common missteps: Knowing where others often make mistakes — and working with a professional who has seen them in the field — can help you avoid problems in your fire stopping system.
- Building inspections: Stay compliant by conducting inspections from certified professionals when required.
- Heating, ventilation and air conditioning (HVAC) concerns: Since HVAC systems connect to building compartments, you must include them in your fire safety plan. Regular inspections, repairs and cleanings can help you maintain the reliability of the HVAC system and fire dampers.
Fire Stop Installation and Professional Services From Alliance Environmental
Fire stopping is a critical element of any building, but the right solution for a project depends on many factors, such as the substrates and applicable standards. You’ll also need to regularly check your fire stop system to ensure continued efficacy and compliance. Working with fire stop installation and maintenance professionals can help you achieve expert implementation and upkeep. Protect your building occupants with services from the fire protection specialists at Alliance Environmental.
With over 25 years of experience and 13 locations across the Western United States, we’re a trusted provider for many diverse businesses. Our services include fire stopping installation, regular inspections, cable organization and compliance checks. We can also help with other elements of your fire protection solution, like fire doors, sprinkler cleaning and HVAC systems.
Request a quote today to start improving fire safety with the experts at Alliance Environmental.
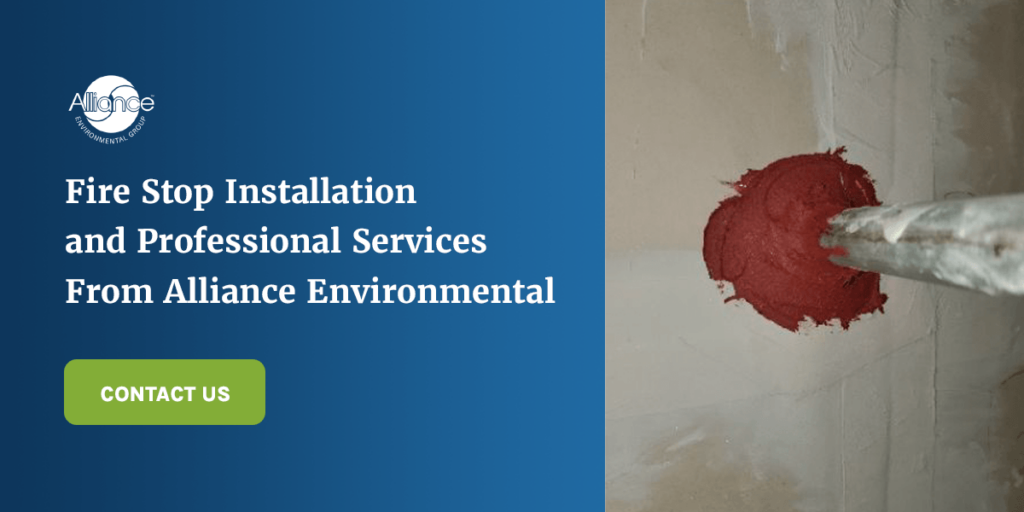