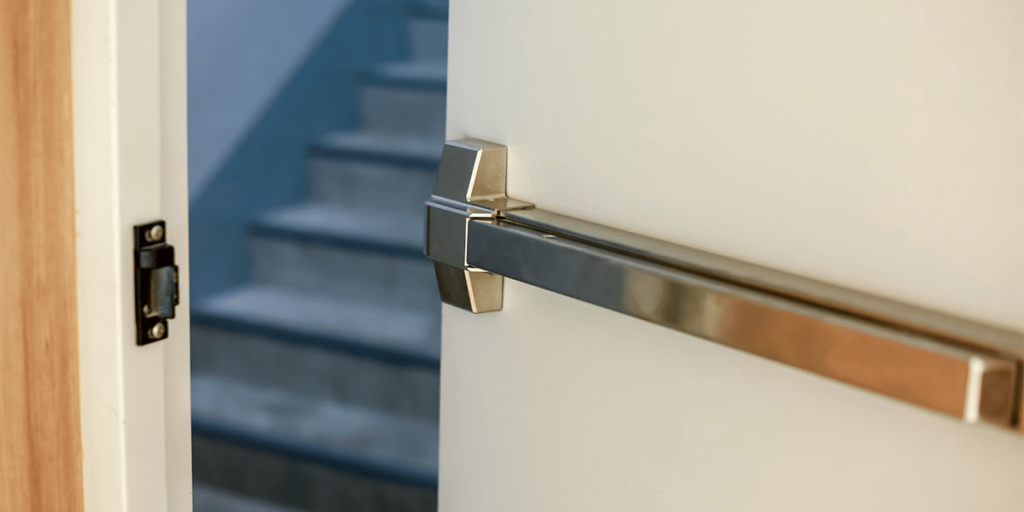
Fire safety regulations outline a wide range of mechanisms for reducing the spread of flames and smoke. One of these mechanisms is fire doors, which keep fires contained in one area while providing a safe exit route.
These doors are crucial in healthcare facilities and other commercial buildings. They contribute to the safety of patients and other occupants, allowing for more controlled evacuation. Fire doors must comply with regulations, including an annual inspection, to perform this job well.
Businesses can fail their fire door inspections due to common issues, such as wide gaps or improperly rated hardware. Since these inspections improve safety and are required by the National Fire Protection Agency’s (NFPA) standards, maintaining compliance is essential. NFPA 101 — which is used nationwide in building and fire safety codes — references NFPA 80, the standard requiring annual fire door inspections.
Let’s explore some common compliance issues and how to prevent these frequent fire door inspection problems during your next evaluation.
5 Common Faults Found in Fire Door Inspections
Building owners can fail fire door inspections for several reasons, many involving a lack of upkeep or improper component selection.
1. Excessive Clearance Around Door Edges
One of the more challenging elements of ensuring compliance is making sure the fire door has proper clearance at its edges. If this space is too large, smoke can easily pass through. A wide gap can also prevent the door latch from engaging, causing the door to open during a fire and contribute to its spread through a building.
The gaps between the door and its frame cannot exceed 1/8 inch. The clearance requirements apply to the top, hinge and lock sides of the door.
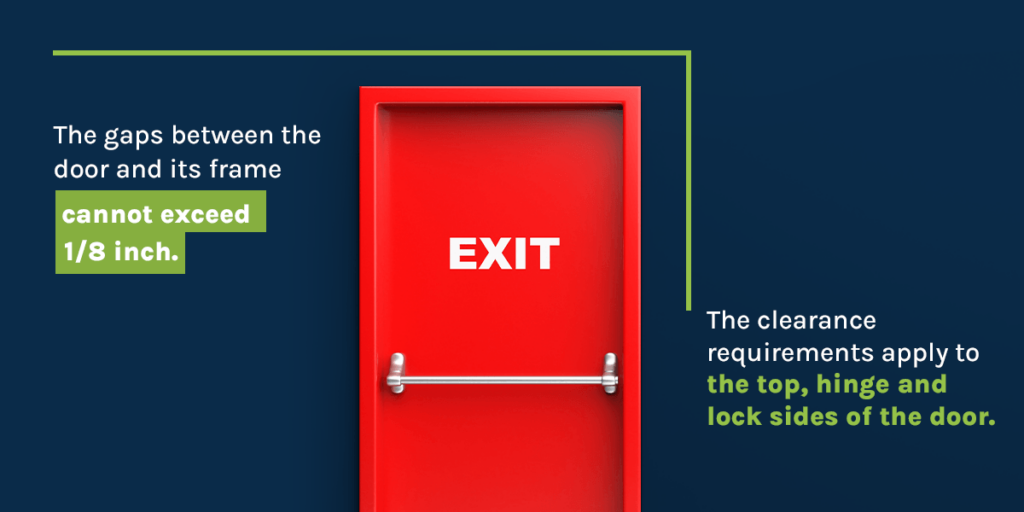
2. Missing, Damaged or Improperly Installed Hardware and Signage
Many smaller components come together to create an effective, functional fire door. Without these elements, you might not pass a fire door inspection. Hardware, such as hinges and panels, could become damaged over time or even go missing. Avoid problems during your inspection by inspecting and repairing these components as needed.
Fire doors must also have appropriate signage and labeling. Signs and labels cannot be missing or covered up. All attached signage should use adhesives — not screws or nails — and take up 5% or less of the door’s surface.
3. Improperly Rated Hardware
Even if a fire door’s hardware is present, in good shape and properly installed, it must have the right rating to withstand fire conditions. All hardware, including panic hardware, must be fire-rated to ensure it does not warp or otherwise deteriorate during a fire.
Below are a few hardware items to consider before a fire door inspection:
- Hinges: Hinges need appropriate ratings to withstand high heat. Hinges that warp from high temperatures could cause the door to open or fall from its frame.
- Panels: Panels commonly lack appropriate fire ratings. Regular glass panels, for instance, might break and allow smoke to move through the doorway, but fire-rated glass leaves intumescent material behind to prevent this situation.
- Panic hardware: Panic hardware also needs appropriate fire ratings, along with clear labeling to identify it as panic hardware.
- Fasteners: Select all fasteners precisely for the items they hold. Fill up unused fastener holes left after changing or removing hardware with steel fasteners. Alternatively, you can fill them with the same material as the door or frame or fire door caulk designed for the job.
4. Insufficient Sealing
Intumescent seals are another component that often causes failed fire door inspections. These seals expand in the presence of heat to fill gaps and prevent smoke from moving through the doorway. If the seals are worn, missing or improperly fitted, they may not effectively prevent the fire’s movement.
Large gaps between the door and walls can also cause ineffective intumescent sealing. The gaps can create a space too wide for the material to fill, preventing it from creating a seal. You’ll need sealant in any areas that could create a gap for airflow, such as around glass panels or between air grills.
Inspect intumescent sealants regularly, as tears and damage can impede functionality. Replace this material as needed.
5. Items or Hardware Impeding Functionality
Even if a fire door is functionally in good shape, nearby objects can prevent it from working properly. Do not block a fire door or keep it propped open when not in use. Items like furniture or equipment can add to a fire and increase the fuel load on the door, potentially causing failure.
Avoid using additional hardware that could impede a fire door’s ability to close and latch properly. Any mechanisms used to prop open a door should be fire-rated and electronically tied to the fire detection system.
Who Performs Fire Door Inspections?
Annual inspections under NFPA 80 require building owners to conduct and document a thorough review of fire doors. This process resembles the one used for other elements like fire alarms and sprinkler systems.
While the standard does not specify a particular certification, NFPA 80 requires someone with an appropriate background in the subject matter, work or project to perform the inspections. This individual typically has a certificate, degree or extensive training.
Since these inspections are crucial for safety code compliance, building owners often outsource inspections to specialized inspectors who stay up-to-date on new trends, best practices and documentation requirements. These professionals can eliminate the guesswork of performing inspections in-house.
Some elements reviewed in fire door inspections include:
- Proper labeling, identification and documentation.
- Appropriately rated components, such as hinges and panels.
- Damaged or worn materials that could affect the door’s functionality.
- Compliant hardware installation and door clearance measurements.
- Operational testing to ensure performance during a fire.
- Sufficient sealing mechanisms, including intumescent seals, to prevent smoke from passing through.
Ideally, your inspector will recommend next steps, such as repairs or product replacements. If your inspection provider offers other fire safety services, they can also ensure consistency and quality in making those necessary changes.
Maintain Fire Door Compliance With Alliance Environmental
Fire doors are an essential safety feature in health care facilities and other commercial buildings. Inspections help ensure performance when it matters most. At Alliance Environmental, our knowledgeable team can help with a comprehensive collection of fire safety services, including fire door inspection, repair, recertification, relabeling and replacements.
We evaluate everything from local fire codes and testing results to label verification and clearance measurements. Then, we provide actionable recommendations to keep fire doors compliant and effective.
Our skilled technicians have multiple certifications, including those from the International Fire Door Inspector Association. We serve diverse businesses across the West Coast, such as healthcare facilities, multi-family housing and industrial companies.
Request a quote today to learn more about how we can help you maintain certification and safety in your business.
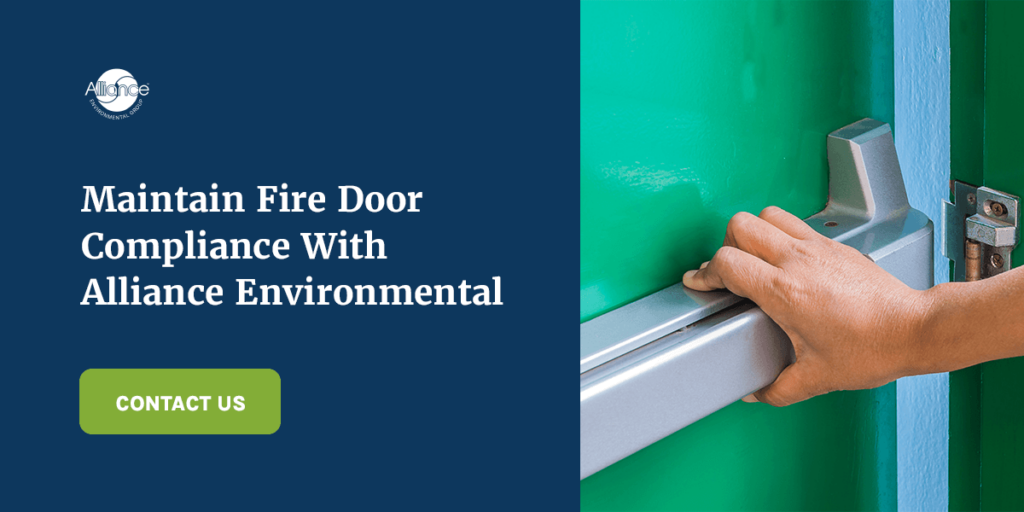